Before setting any new goals or targets, perhaps start by asking some key questions:
- Has our budget for safety and PPE changed?
- Are we manufacturing new lines/products/parts?
- Are new types of PPE required that weren’t last year?
- Are we expecting a significant number of new employees this year?
- Have there been any changes to applicable EN safety standards?
Reviewing your current procedures, department functions and carrying out fresh safety assessments will help to identify any changes that may need an increase in PPE spend, new items of PPE to be sourced, old lines of PPE to be discontinued and perhaps even additional personnel in the safety department.
Here are our top 10 areas you can set goals in to create a culture of safety first, reduce injuries and keep PPE costs down:
1) Conduct a full site PPE inspection
Carry out a comprehensive review of all departments where there are hazards and assess the current issued PPE to ensure it is fit for purpose. Employees should also inspect their PPE daily to look for any signs of deterioration or failing and replace only if necessary.
2) Create safety metrics for all departments to achieve
Setting a company-wide safety goal is great, but it will be difficult to achieve if employees don’t know how they’re doing. Creating a safety metrics display and putting it in a prominent place with regular updates will encourage staff to play their part.
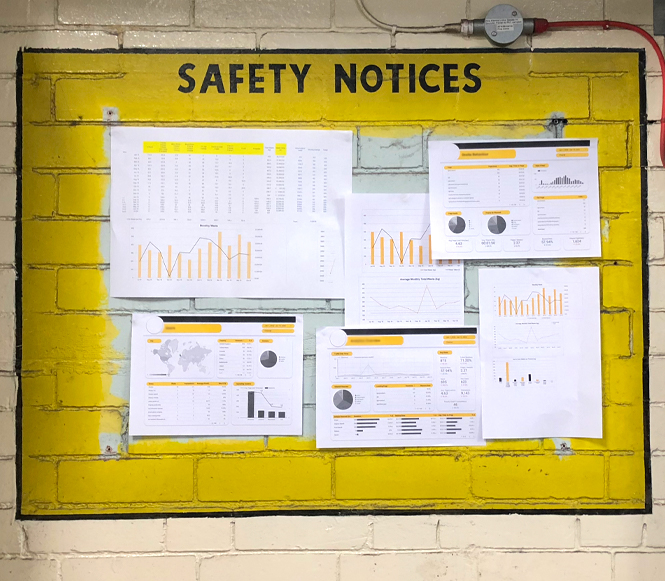
3) Hold regular safety meetings
If you don’t already, it’s a good idea to start holding regular safety meetings with the relevant staff from each department. It will improve safety compliance, allow staff to feel involved and reduce the likelihood of incidents reoccurring.
4) Prioritise addressing the no 1 injury in your organisation
Focus on eliminating as many of the hazards relating to the no 1 injury in the business as you can. This will help you to reduce the no injuries faster, reduce associated costs and make staff feel safer when incidents do come down.
5) Create a system for reporting safety hazards
Design and roll out a simple system for all employees to identify and report a hazard or issue they feel could be a potential safety concern. This could be through posters, a dedicated email address or a suggestion box.
6) Reward safe behaviour and attitudes
Acknowledging and rewarding safe behaviour and achieving safety metrics can be hugely motivating for employees and encourages continued participation in your safety program. This can be done in a number of ways be it congratulations on social media, a prize or a certificate.
7) Support and participate in safety awareness campaigns
There are several national and international safety awareness campaigns and organisations dedicated to helping businesses operate safely including the British Safety Council, NEBOSH, rospa and The British Safety Industry Federation.
Tilsatec are members of the BSIF, the lead association for the Personal Protective Equipment (PPE) Directive and recognised as a Competent Authority by the Health & Safety Executive (HSE). Tilsatec are also proud members of the RSSS Registered Safety Supplier Scheme.
Companies displaying the scheme’s logo have signed a binding declaration that the safety equipment they offer meets the appropriate standards, fully complies with the PPE regulations and is appropriately CE marked.
Ensuring you only purchase your PPE from a member of the RSS scheme provides reassurance that you are buying from an approved, reputable manufacturer or supplier.
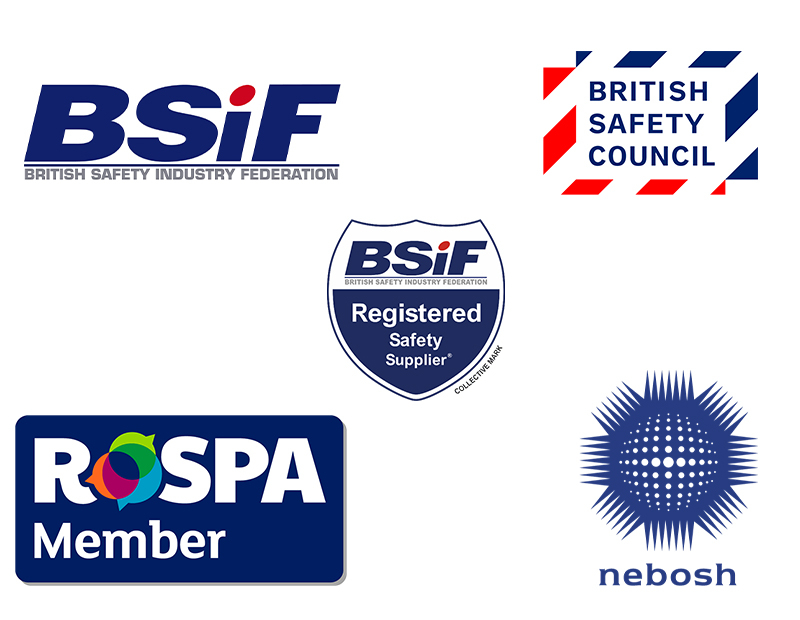
8) Carry out accident investigations
Ensure you have a thorough procedure with a dedicated staff member to investigate fully when an accident occurs. PPE is the last line of defense, but it does not guarantee injury prevention.
Identify the cause of the incident and put measures in place to prevent the same incident from reoccurring.
9) Deliver regular and engaging safety training
You may already have a set of training manuals or content in place, but might this be the year you review it?
If staff are not engaged or feeling like they want to interact and get involved, it’s likely the messages you want to get across are not being heard. Lots of training providers can make safety learning fun and interesting.
It’s also important to ensure every new employee gets a comprehensive safety induction before being allowed to operate machinery or even be allowed on to the production floor.
10) Get frequent feedback on your safety program
Sending out a brief survey to each department allows employees the opportunity to have their say and it provides important feedback on how well the safety program is working. Employees are far more likely to engage and participate if they’ve had a say in how it runs.
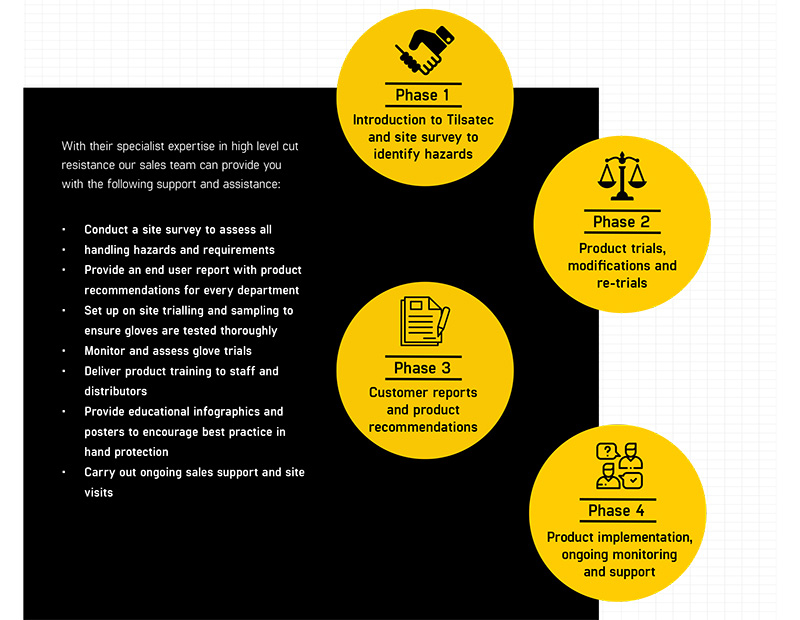
When it comes to identifying and specifying the right hand protection for your workforce, it can seem overwhelming looking at the number of protective gloves now in the market place. Our Hand Protection Evaluation Process is clear, tried and tested, designed to guide you every step of the way and support you beyond your initial selection stage.
Click here to find out how our Hand Protection Evaluation Process can benefit your business and you can view our range of high performance hand and arm protection solutions here